As grandes fabricantes do setor de pavimentação asfáltica estão aproveitando o cenário favorável para investimentos do segmento de máquinas e construção para posicionar produtos com atualização tecnológica e melhor performance. Neste Comparativo, a EaeMáquinas traz detalhes das soluções apresentadas por quatro fabricantes renomadas que foram destaques na M&T Expo em novembro do ano passado. Confira qual a melhor solução para suas aplicações asfálticas.
AMMANN ACM 140 PRIME
O destaque da Ammann é a usina ACM 140 PRIME considerada o carro-chefe da fabricante que já comercializou mais de 170 unidades para o mercado Latino Americano, o que fez a Ammann do Brasil ser agraciada em 2017 e 2018, consecutivamente, com o Prêmio Exportação (RS), oferecido pela instituição ADVB/RS. A premiação foi concedida em função do destaque setorial em máquinas e equipamentos, um reconhecimento da excelência de desempenho em termos de exportação, além do reconhecimento de um importante caminho obtido que reflete a demanda por misturas asfálticas de alta qualidade e de usinas de asfalto reconhecidas mundialmente.
A unidade brasileira do grupo Ammann se destaca por sua localização geográfica o que a torna versátil para o fornecimento de soluções para construção de estradas e rodovias para toda as Américas.
Prova disso são as Usinas de Asfalto contínuas modelos ACM 100 PRIME e ACM 140 PRIME, usinas com capacidade produtiva de 100 t/h e 140 t/h, respectivamente. E a produção das usinas gravimétricas ABC 140 SOLID BATCH e ABC 180 SOLID BATCH, usinas com capacidade produtiva de 140 t/h e 180 t/h. As Usinas de Asfalto Ammann série PRIME (ACM 100 PRIME e ACM 140 PRIME) e da série SOLIDBATCH (ABC 140 SOLIDBATCH e ABC 180 SOLIDBATCH) reúnem todos os conceitos de alta qualidade e excelência em produção asfáltica, quando se fala em produção asfáltica contínua ou por lote, desde o desenvolvimento do produto, a utilização dos componentes chaves do sistema, com o conceito integrado (incluindo controles, tambor-secador, queimador, misturador e filtro), assim a Ammann oferece aos clientes uma solução completa e otimizada.
Outro destaque é a produção nacional das usinas gravimétricas ABC 140 SOLIDBATCH e ABC 180 SOLIDBATCH, que marcam a produtividade no Brasil e América Latina, pela excepcional precisão dos materiais peneirados e classificados. O processo de aquecimento e secagem dos agregados, destaca-se pelo queimador suíço especialmente adaptado ao processo de secagem e aquecimento, disponível em todas as combinações possíveis de combustível (óleo pesado, diesel, gás natural, gás liquefeito de petróleo, entre outros).
Trata-se de uma parte fundamental, a fonte de energia e de alto rendimento garantindo o máximo aproveitamento do combustível e baixo nível de contaminação, assim como o mais baixo nível de consumo de combustível por tonelada de asfalto produzida no mercado. O portfólio de produtos da Ammann do Brasil é complementado com a linha de pavimentadoras de asfalto, em uma ampla gama de modelos, ao todo 17 modelos com capacidade de produção de 35 a 1.100 t/h e largura de pavimentação de 800 mm à 14 metros.
A linha de compactação o portfólio inicia com os compactadores de percussão de 30 kg, os rolos de trincheira controlados por controle remoto infravermelho, passando pelos rolos tandem de 1,5 a 11 toneladas nas versões de cilindro duplo e combinado (cilindro e pneus), em a compactação pesada de solos inclui compactadores monocilíndricos de 4 a 22 toneladas, terminando a linha de compactação com rolos pneumáticos com capacidade de compactação de até 28 toneladas e controle de pressão de ar através da cabine de operação.
Os diferenciais tecnológicos, como as unidades e os sistemas de controle, asfalto de baixa temperatura, consumo energético, desgaste dos materiais e combustíveis alternativos, são alguns benefícios oferecidos ao setor de mobilidade que garantem a máxima produtividade, nas mais diversas situações e lugares. Com isso, compradores do mundo todo podem confiar nesta marca global que tem seu foco no cliente, graças à qualidade, capacidade inovadora e credibilidade.
A história da Ammann é de inovação. As dezenas de patentes que a empresa assegurou em seus 150 anos de existência comprovam esse ponto. A busca pela inovação já estava em andamento em 1908, quando a Ammann recebeu uma patente para uma máquina de macadame – essencialmente uma combinação de uma usina de mistura de asfalto e uma pavimentadora. A máquina usava o que era uma tecnologia revolucionária na época para eliminar um perigo emergente à saúde – a poeira expelida pelos automóveis. As usinas de asfalto da Ammann utilizam a tecnologia para permitir a produção com porcentagens extremamente altas de materiais reciclados.

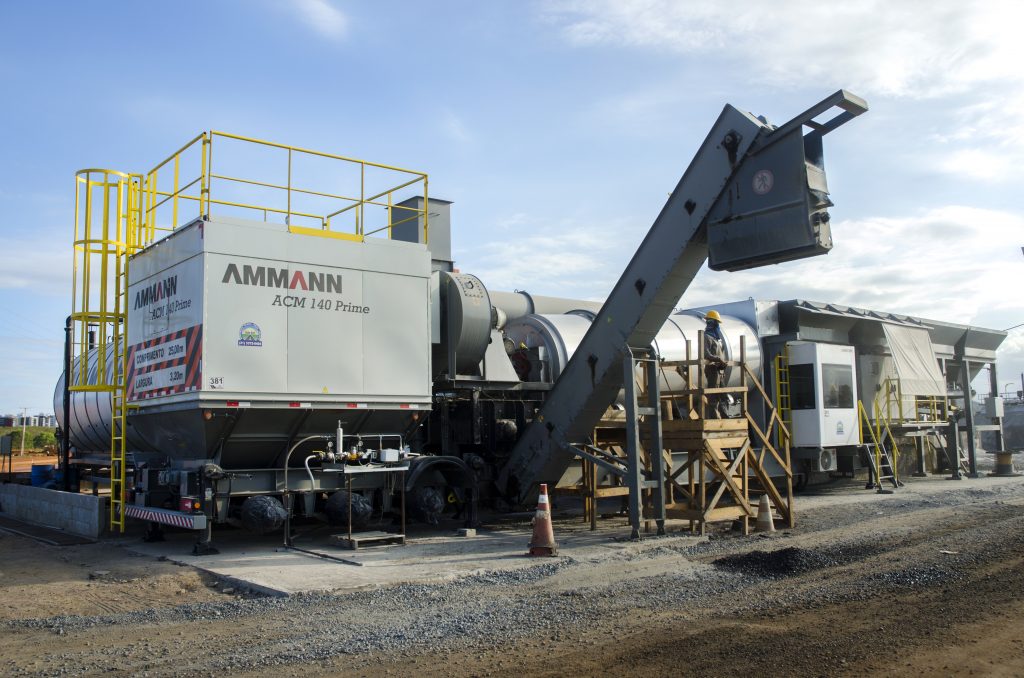
BOMAG-MARINI MAGNUM 120 MAX
As usinas BOMAG MARINI Latin America, fabricadas no Brasil, contam com quatro modelos de usinas de asfalto do tipo contínua contrafluxo, configuradas em chassi único. A MAGNUM 120 MAX, por exemplo, é o modelo com capacidade de produção de até 120 toneladas por hora, ideal para projetos de médio porte.
Entre os principais diferenciais das usinas MAGNUM 120 MAX está a capacidade de processamento de RAP, de até 30%. O sistema de mistura externo rotativo, que permite a execução de todos os tipos de misturas asfálticas, desde a utilização de ligante asfáltico convencional, até asfalto modificado com polímeros, asfalto borracha, misturas quentes e asfalto morno WMA. Sendo internacionalmente reconhecido e atestado para misturas especiais e oferecendo a maior flexibilidade de layout da categoria por permitir a incorporação de filler e fibra em diversas posições.
Também devemos destacar que as usinas MARINI Latin America possuem uma quantidade menor de partes mecânicas e de dispositivos eletrônicos, o que reduz significativamente os custos de manutenção e proporciona um consumo de energia menor, além disso, todos os componentes, consolidados no mercado, são comercializados mundialmente e estão sempre acessíveis aos clientes, diminuindo custos e tempo de máquina parada.
Para garantir a excelência na produção de massa asfáltica, é necessário que o posto de operação seja ergonômico e ofereça as condições ideias para um resultado produtivo, por isso, a cabine de operação da MAGNUM 120 MAX oferece todo o conforto e espaço que o operador necessita para realizar um trabalho eficiente e seguro, além de contar com um painel de controle simples, intuitivo e moderno, o qual otimiza a operação, eliminando paradas indesejadas e proporcionando maior produtividade.
O software EASY MANAGER gerencia a correia dosadora através da variação na pesagem da célula de carga centralizada individual, por este motivo, tem controle total no processo de dosagem dos materiais inertes. Além dos 3 silos padrão, é possível incluir o 4° silo como opcional. O vibrador, padrão no silo 1, também pode ser adicionado a todos os silos. A comunicação do sistema ocorre em rede CANopen, para que o trafego de informações da máquina ocorra de maneira inteligente e eficiente no processo de produção de massa asfáltica.
Nas usinas MAGNUM 120 MAX, a secagem e o processo de mistura dos agregados com o ligante ocorrem fora do secador, em seções distintas e, por isso, não há transferência de calor da zona de secagem para a zona de mistura, além disso, proporcionam economia de energia e uma redução significativa de custos, uma vez que os acionamentos do tambor secador movimentam também o misturador.
O misturador externo rotativo possui alta potência mecânica para o processo da mistura, contando com aletas dentadas, onde o material permanece retido na parte inferior do misturador, recebendo um elevado número de golpes com forte intensidade, gerando uma alta energia mecânica para o processo de mistura, e por consequência, produzindo uma massa asfáltica homogênea e de excelente qualidade. O design do misturador, com aletas e revestimentos do fundo aparafusados facilita a manutenção e reduz o custo operacional. Estes componentes são fabricados em aço de alta resistência a abrasão e oferecem uma vida útil quatro vezes maior em relação ao misturador Pugmill tradicional. Além de oferecer o maior tempo de mistura, resultando em maior homogeneidade com a completa cobertura dos agregados pelo ligante.
A mistura ocorre em duas etapas, o que proporciona uma excelente qualidade de mistura. Na primeira etapa, ocorre a injeção de ligante através de um sistema único de espargimento e união deste com os agregados maiores, e na segunda etapa ocorre a adição dos agregados finos na mistura de forma a garantir a homogeneidade da massa asfáltica.
Segundo a fabricante, as usinas MARINI Latin America possuem a maior capacidade de processamento de RAP (Reclaimed Asphalt Pavement) da categoria, unindo eficiência, sustentabilidade e economia, elas são capazes de processar até 30% de RAP. O design do secador garante que o RAP não entre em contato com a chama do queimador, sendo aquecido por condução térmica através de uma câmara interna e posteriormente adicionada à mistura.
O filtro de mangas conta com mangas em tecido NOMEX e lisas de poliéster, com temperatura máxima de trabalho de 210° e 150°, respectivamente. O caracol de retorno de finos do filtro de mangas possui a inclinação ideal, o que proporciona durabilidade e confiabilidade, sem retornos por desgaste no excesso de inclinação. Além disso, a manutenção é simples e econômica, a reposição é facilitada devido à ampla rede de distribuidores e o valor unitário para troca das mangas é significativamente menor do que as mangas fabricadas em material importado. As usinas MAGNUM 120 MAX não necessitam de damper de ar frio, uma vez que o controle de temperatura dos gases é de altíssima eficiência.
Manutenção facilitada. Além de possuir abertura para todas as partes de manutenção, as usinas MAGNUM 120 MAX contam com um design inteligente, que oferece fácil acesso a cada ponto de inspeção.
Além da 120 MAX, essa série conta com outros três modelos de diferentes capacidades, oferecendo uma gama completa para qualquer necessidade: MAGNUM 80 MAX, MAGNUM 140 MAX e MAGNUM 160 MAX. Além da série MAX de usinas contínuas contrafluxo, configuradas em chassi único ou bipartido como opcional, a MARINI Latin America traz para o mercado a nova modalidade de usinas de asfalto para consolidar a chegada do futuro dos equipamentos de produção de mistura asfáltica (CBUQ), através da série CARBON T-BOX, com usinas contínuas contrafluxo configuradas em contêiner padrão ISO.
De modo geral, a produção de asfalto utiliza materiais classificados entre ligante asfáltico e agregados naturais ou artificiais. O ligante asfáltico é um ligante betuminoso derivado da destilação do petróleo, que atua como um adesivo impermeável e de pouca reatividade. Os agregados naturais, como brita e areia, são alcançados através de diversos processos. Para obter uma boa qualidade em uma pavimentação, alguns fatores devem ser levados em consideração, como a qualidade do projeto, visto que ele deve estar de acordo com a realidade do local, considerando fatores como o clima da região.
A escolha dos materiais deve ser realizada avaliando sua qualidade, a fundação deve ser apropriada para o tipo de projeto, bem como o tipo de mistura asfáltica e camadas, além disso, a construção deve ser realizada de forma correta, seguindo as orientações técnicas. Outro ponto importante no resultado final é a manutenção, que deve ocorrer periodicamente de acordo com a recomendação do projeto do pavimento.
Através do RAP (Reclaimed Asphalt Pavement), o produto da remoção e trituração das camadas asfálticas deterioradas pode ser reutilizado para elaboração de novas estradas. Para isso, as usinas precisam possuir o anel de RAP, e com isso, asseguram uma mistura seca durante a troca térmica entre os agregados virgens e o material reciclado.
Para obter uma boa qualidade de RAP, devem ser considerados alguns pontos cruciais: evitar a contaminação do material durante os processos de fresagem, transporte e armazenamento; realizar a caracterização detalhada do RAP; obedecer às normas e seguir as recomendações de experiências internacionais; realizar ensaio detalhado do traço da mistura e desempenho da mistura; estabelecer o controle de qualidade da usina como um item indispensável na obtenção do material.
A utilização dos revestimentos asfálticos pode variar dependendo do tipo de obra e da região, o revestimento mais comum no Brasil é o CBUQ (Concreto Betuminoso Usinado a Quente), ele é composto por diversos agregados e CAP, e deve ser usinado por máquinas adequadas para realizar a dosagem precisa de seus componentes, a secagem dos agregados, e, posteriormente, a mistura de maneira homogênea dos agregados e CAP.
Além do CBUQ, outro revestimento utilizado é o PMQ (Pré-Misturado a Quente), esta mistura é formada por agregado graduado, cimento asfáltico e posteriormente, é espalhada e compactada. O PMQ é adequado em camadas de regularização, camadas de ligação, base ou binder. O PMF (Pré-Misturados a Frio) é uma mistura usinada proveniente de agregados graúdos, miúdos e de enchimento, eles são misturados com EAP (Emulsão Asfáltica de Petróleo) em temperatura ambiente, e pode ser utilizada em revestimento de ruas e estradas com baixa incidência de tráfego, em reparos e manutenções, e também como camada intermediária.
A principal diferença entre estes revestimentos é que entre as misturas quentes (CBUQ e PMQ) o controle da mistura é realizado através da análise de suas propriedades, sendo que no caso do CBUQ este controle é realizado de maneira mais rígida. Comparando o CBUQ e PMQ com o PMF, a principal distinção é em relação ao ligante asfáltico, visto que no caso da mistura a frio (PMF), a EAP é utilizada no lugar no CAP.
A fábrica BOMAG MARINI Latin America está situada na cidade de Cachoeirinha no Brasil e desde 2013 pertence à divisão de construção rodoviária do Grupo FAYAT, fornecedor de uma ampla gama de equipamentos de construção rodoviária, que também tem o know-how de outras fábricas de prestígio como a MARINI (Itália) e a BOMAG (Alemanha). Assim, todas as equipes do grupo FAYAT usam tecnologias avançadas e atendem aos critérios mais exigentes em termos de confiabilidade, segurança, rentabilidade e proteção ambiental.
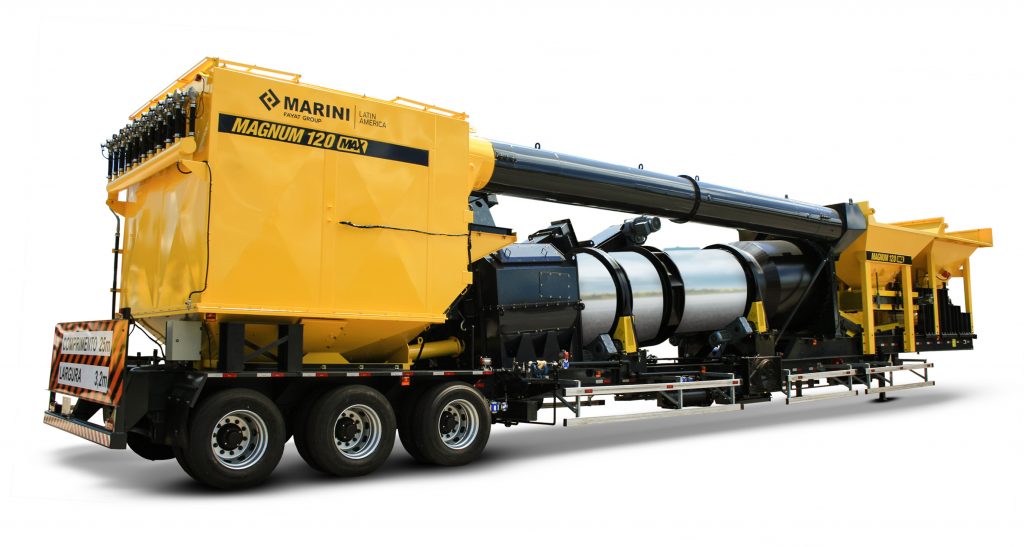
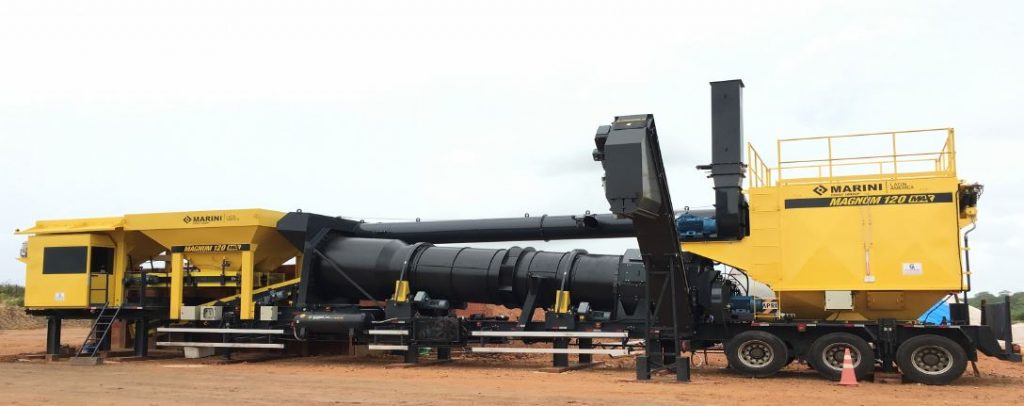
CIBER SÉRIE iNOVA
A Ciber Equipamentos Rodoviários está lançando a linha completa da nova serie iNOVA de usinas de asfalto. Com produção variando de 50 até 200 t/h, a nova linha é perfeita para todos os tipos de obras, desde obras de pequeno porte até obras de grande porte onde alta produção diária é requerida. No que tange a conceito e tecnologia, os 4 modelos da série apresentam diversos destaques, seguindo a tendência da Ciber de sempre disponibilizar ao mercado equipamentos de alto valor agregado.
A nova linha já cumpriu com mais de 2 anos de testes antes de ser comercializada a fim de garantir a perfeição nas funcionalidades do equipamento. A iNOVA 2000, primeira usina a ser fabricada da série já está presente em 3 continentes. Os 4 modelos em destaque são: iNOVA 1000+ iNOVA 1500+ iNOVA 1502+ iNOVA 2000.
As principais características da nova série estão resumidas em 5 grandes destaques relacionados com facilidade logística e baixo custo de transporte, tecnologias que reduzem o consumo de combustível e que permitem produção de diferentes tipos de misturas com qualidade e produtividade constantes, harmonia entre sofisticados sistemas eletrônicos e uma operação simples e intuitiva e com baixo nível de manutenção e entregando robustez, confiabilidade e segurança durante a operação. Os 5 destaques estão descritos abaixo.
A Ciber é reconhecida internacionalmente por suas usinas móveis construídas sobre semitrailers. Apenas conectando o pino rei do semi-trailer da usina a um caminhão é possível transportar o equipamento da fábrica para o canteiro de obras ou entre canteiros de obras. Com a nova serie iNOVA o conceito de mobilidade foi levado ao extremo. As usinas apresentam 1 ou 2 mobilidades, dependendo do modelo, resultando em uma ótima relação entre produção e o número de mobilidades.
A vantagem de uma usina compacta altamente produtiva está no baixo custo de transporte (terrestre e marítimo) e instalação, além de flexibilizar a instalação em locais mais restritos. Outra característica importante é o grande range de produção das usinas desta linha, sendo capaz de produzir a uma taxa de 50% da máxima, sem prejudicar a qualidade da mistura ou incorrer em aumento de custos de produção. Como consequência, há uma grande flexibilidade de produção conforme a logística disponível durante a produção (quantidade e tamanho das caçambas dos caminhões e velocidade de aplicação). Em produção de até 50% abaixo da nominal, a qualidade é mantida constante graças principalmente as novas tecnologias empregadas do queimador, tambor secador e misturador.
Os custos de produção das misturas asfálticas estão diretamente relacionados com a lucratividade do construtor que fabrica a mistura na usina, ou seja, o cliente Ciber. O custo com o combustível é bastante relevante e normalmente representa o terceiro maior impacto (atrás do custo do Cimento Asfáltico de Petróleo e dos agregados). Consciente da influência do combustível no negócio de nossos clientes, a Ciber investiu em tecnologias que visam minimizar o consumo de combustível. Das tecnologias implementadas na nova linha destaca-se o isolamento térmico do tambor secador, o novo queimador total air em malha fechada e o sistema de troca de calor inteligente.
Queimador Total Air em malha fechada
A nova tecnologia de queimadores Ciber controla, de forma acurada e automática, a relação ótima entre ar e combustível necessária para a combustão. Nesta tecnologia, todo o ar para a queima é provido mecanicamente pela usina (sem sucção de ar do meio ambiente) através de dois ventiladores (um soprador e um ventilador axial). Denominado Total air, este queimador trabalha em malha fechada atuando, automaticamente e constantemente, na intensidade da chama buscando sempre a temperatura ideal da mistura asfáltica, determinada pelo operador.
Troca de calor inteligente
A energia térmica produzida pelo queimador da usina (a chama e os gases de combustão) deve ser aproveitada ao máximo pelos agregados que, por sua vez, precisam estar secos e aquecidos para que haja adesividade com o ligante asfáltico no processo de mistura. Mantendo a energia térmica em nível constante, quanto mais energia os agregados recebem durante o percurso no tambor secador, menor será a temperatura dos gases a jusante. O inverso também é verdadeiro, ou seja, quanto maior for a temperatura dos gases após o secador, menos energia os agregados receberam da fonte de calor. Sabe-se também que a temperatura dos gases no filtro de mangas (após o secador) deve ser maior ou igual a 100°C para evitar condensação da água na caixa de filtro e prejudicar o processo de combustão gerar um alto índice de manutenção. Logo, quando a temperatura dos gases no filtro for igual a 100°C teremos a melhor trocar de calor possível entre os agregados e a fonte de calor e também temperatura adequada dentro do filtro. Com base neste princípio, a última geração de usina Ciber consegue controlar automaticamente a temperatura dos gases no Filtro de mangas através da variação da velocidade de giro do secador e, assim garantir, independentemente das características dos agregados e mistura, a perfeita troca térmica. A consequência é a garantia do menor consumo de combustível possível para cada condição específica.
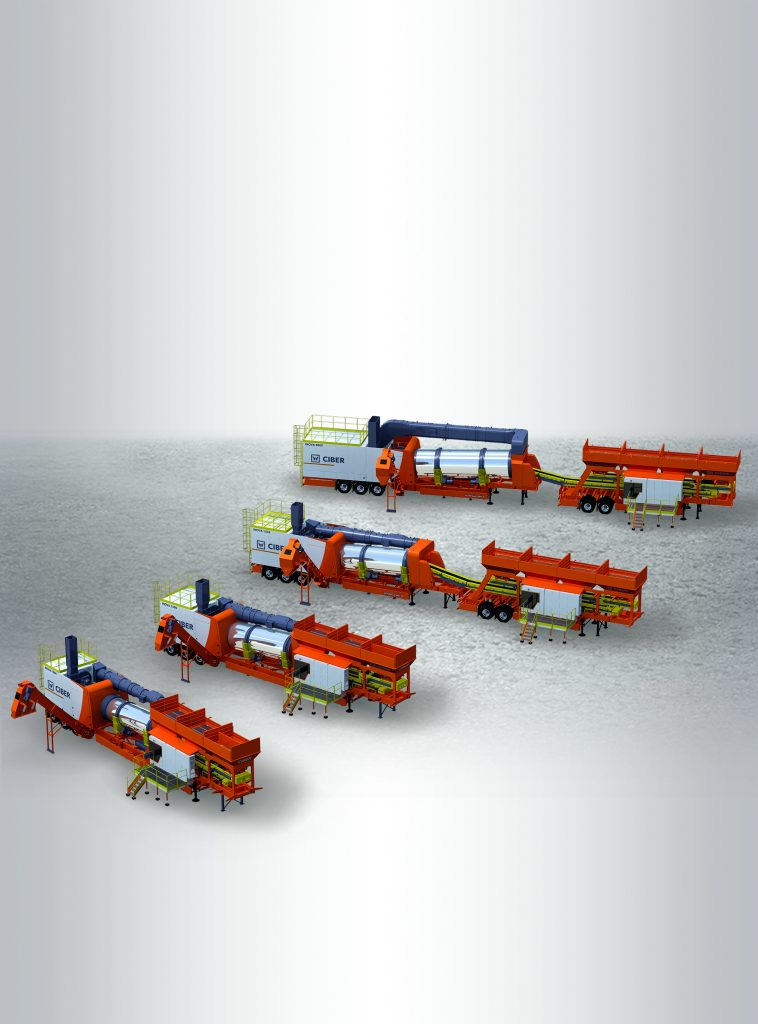
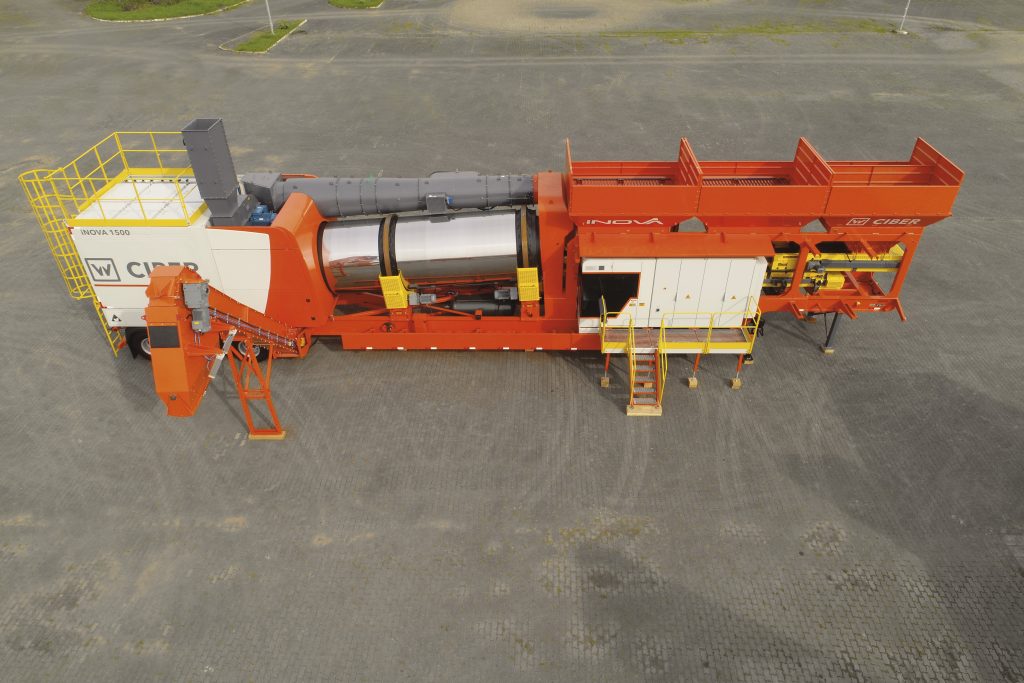
LINTEC LX12000
A Lintec-Ixon vem se destacando nos últimos anos por disponibilizar uma ampla variedade de Usinas de Asfalto, são equipamentos de 40 até 160 t/h, com grande destaque para a usina LX12000 com capacidade de 120 t/h.
A LX12000 da Lintec-Ixon tem como destaques a versatilidade de uma usina móvel, excelente capacidade de produção e uma excelente relação custo x benefício. Possui dosadores de agregados em linha, que ajudam a evitar contaminação cruzada e podem ser expandidos de acordo com a necessidade do cliente, secador com grandes dimensões que garante o melhor tempo de permanência para troca térmica, com aletas removíveis que permitem ajustes se necessário.
Outra característica importante da LX 12000 é seu misturador externo duplo eixo, componente ideal para a eficiência da mistura asfáltica. Permite a adição de aditivos, controle do tempo de mistura e a manutenção da temperatura durante a mistura por ser aquecido com óleo térmico, os componentes duráveis, fundo e laterais revestidos com elementos resistentes a abrasão garantem maior durabilidade e baixa manutenção do conjunto. Permite ainda a utilização de asfalto reciclado quando equipada com o Dosador de RAP.
A preocupação com o meio ambiente fica evidente na LX12000, o sistema de filtragem extremamente eficiente e com ampla área de filtragem, os elementos filtrantes são lisos e confeccionados em Poliester ou Nomex, tornando sua manutenção simples e econômica.
Outros grandes pontos de destaque da LX12000 são a cabine de comando e o sistema de controle. A cabine é bastante ampla com capacidade de comportar o painel de força, permitindo maior segurança e proteção ao sistema por estar em um ambiente interno livre das intempéries, além de estar em uma região mais limpa da usina, a visão do processo é privilegiada. Já o software de controle é inteiramente desenvolvido pela Lintec-Ixon, com foco na facilidade de operação, segurança dos processos e otimização dos recursos, tudo isso permitindo acesso remoto e uma ampla gama de relatórios ao gestor da planta.
A LINTEC-IXON foi fundada em 1995, sediada na cidade de Santa Rosa, no noroeste do estado do Rio Grande do Sul, Brasil. Ao longo dos anos vem investindo na qualificação de seus colaboradores e atuando no segmento de equipamentos utilizados para a produção de usinas de asfalto e centrais de concreto. O resultado foi um produto superior, de fácil utilização, com pouca manutenção e alta produtividade, o que possibilitou conquistar cada vez mais clientes.
A LINTEC-IXON tem atuado no mercado nacional, bem como no mercado externo, com exportações para a América Latina e África, que tem tido crescente importância nos últimos anos. Sempre buscou a melhoria contínua com o objetivo de oferecer as melhores soluções para seus clientes. Neste sentido, em 2014 passou a fazer parte de uma parceria estratégica com a LINTEC GmbH & Co. KG com sede em Buxtehude, Alemanha, fabricante líder global de usinas misturadoras de concreto e asfalto em contêiner e equipamentos relacionados.
Sendo assim, uniu-se a qualificação e superioridade dos projetos IXON na produção de usinas de asfalto e centrais de concreto, à tradição e experiência da LINTEC na produção de usinas misturadoras de asfalto e concreto em contêineres. Esse é um upgrade ideal para o portfólio e irá aumentar ainda mais o desenvolvimento de produtos LINTEC-IXON no Brasil e expandir suas operações na América Latina.
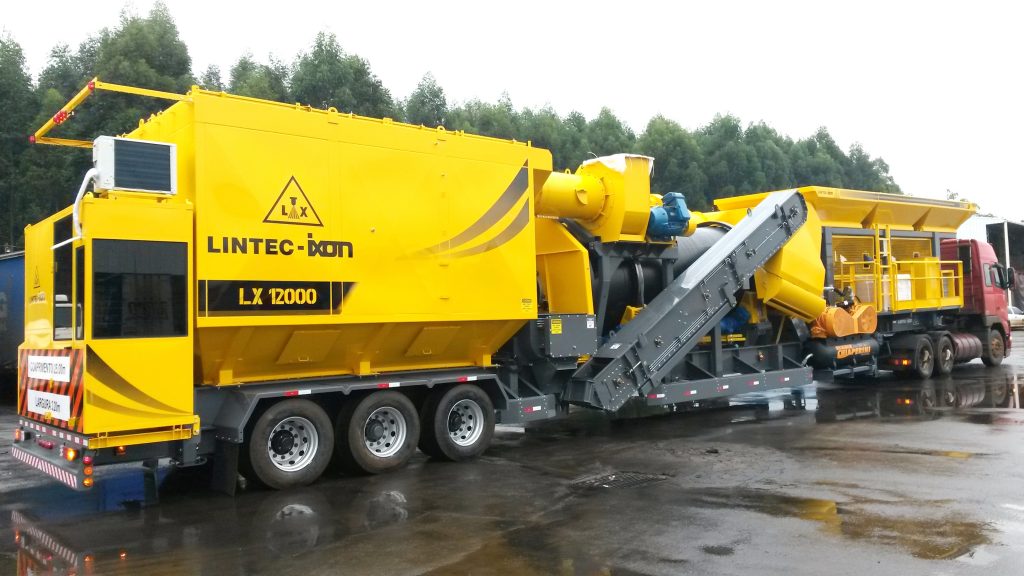
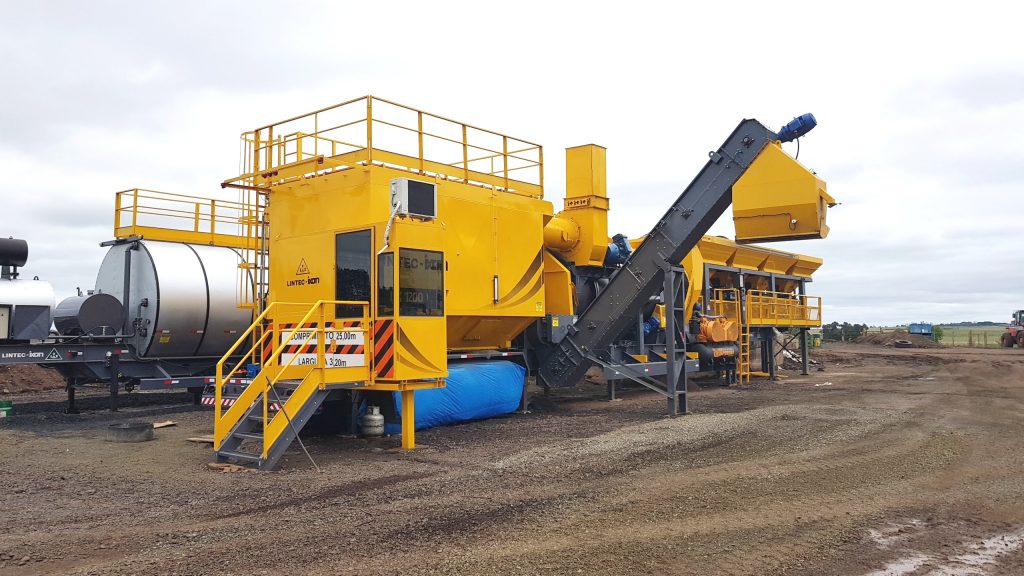