Motores elétricos eficientes na corrida pela descarbonização da indústria siderúrgica
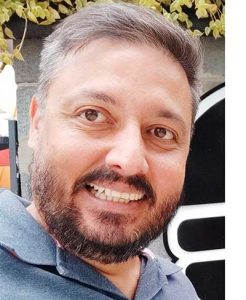
A indústria brasileira do aço, nona maior do mundo, anunciou recentemente expectativas de dobrar consumo da commodity per capita do país dentro de uma década. Hoje, cerca de 125 quilos do metal por habitante são consumidos nacionalmente, volume ainda baixo comparado à média mundial de 230 quilos. A previsão do Instituto Aço Brasil é que esse número chegue a 250 quilos em 10 anos, considerando um ambiente mais propício para investimentos, estimulados principalmente pelas reformas estruturantes. Para a entidade, a demanda pela commodity deve crescer devido à necessidade de construir mais habitações e pelos projetos nas áreas de energia renovável, portos e petróleo e gás.
Ao mesmo tempo em que prevê essa expansão, a indústria do aço no Brasil, assim como a mundial, tem a descarbonização como um dos principais desafios nos próximos anos. O setor de ferro e aço é globalmente o maior emissor industrial de dióxido de carbono, respondendo por entre 7% e 9% do total, de acordo com a Associação Mundial do Aço. Para cumprir as metas mundiais quanto à energia e ao meio ambiente, as emissões de poluentes da indústria siderúrgica precisam cair em pelo menos 50% até 2050, conforme aponta a Agência Internacional de Energia.
E isso será um grande desafio para o setor uma vez que a maior parte da produção de ferro e aço ainda depende de tecnologias tradicionais baseadas em combustíveis fósseis. Ainda hoje, o carvão é usado para gerar calor e fazer coque. Como resultado, o insumo é responsável por atender 75% das necessidades energéticas das siderúrgicas, tornando-as as maiores consumidoras industriais de carvão.
Nesse contexto, investimentos em sistemas de motores mais eficientes podem dar sua contribuição para a redução do consumo de energia. Esses equipamentos, que são usados para executar aplicações como ventiladores, compressores, bombas e laminadores em siderúrgicas, consomem apenas cerca de 7% da energia total. Estima-se, entretanto, que até 70% da energia demandada pelos motores em uma usina siderúrgica seja perdida e desperdiçada devido a ineficiências do sistema.
A modernização dos sistemas de motores resulta em reduções significativas nos custos de energia. Geralmente, as aplicações na fabricação de ferro e aço têm cargas variáveis, o que significa que os sistemas de motores que dependem do controle mecânico de velocidade não estão operando em sua eficiência ideal. A adoção de inversores de frequência (VFD) para controlar motores pode deixar o sistema muito mais eficiente. Adicionar VFDs aos ventiladores de um forno básico de oxigênio, por exemplo, reduz a demanda de energia e os custos associados em cerca de 20%.
Além disso, algumas tecnologias já em uso e em desenvolvimento estão ajudando a indústria a diminuir o uso de combustíveis fósseis em seus processos. Fornos elétricos a arco podem substituir fornos básicos de oxigênio, enquanto o hidrogênio passa a ser usado como agente redutor no lugar de carbono e coque.
Diante disso, a indústria do aço brasileira pode, portanto, almejar metas ambiciosas de consumo no mercado local, ao mesmo tempo em que reduz gastos de energia e segue na sua busca por um futuro Net Zero.
Para mais informações: https://new.abb.com/br